
Integration of Alternative Propulsion Systems – Challenges
and Solutions for Vehicle Manufacturers
- Helfried Müller
- April 25, 2022
- 4-min read
We are probably living through some of the most exciting chapters of the automotive industry since its beginnings: The Electrification. Some automotive manufacturers already have a distinct lead over others in terms of developing non-combustion-based, alternative propulsion systems, depending on their home region’s openness for innovation – and on their level of strategic primary expenses. The underlying goal behind this development? To enable the optimal operational strategy for battery electric vehicles (BEVs) in tandem with a fitting charging strategy.
Electric vehicles already have a 120-year-old history, first emerging in the 1900s. During that time, more than a third of all U.S. registered vehicles had a battery-powered engine. However, as gasoline prices dropped significantly, internal combustion engines (ICEs) quickly outmaneuvered their electric counterparts due to their superior range, faster refueling and lower fuel cost. But this early peak will probably be overshadowed soon, as market observers expect that by 2030 about half of all European new vehicle registrations will be BEVs. The age of alternative propulsion systems has already begun.
> Range and charging are (still) central issues of alternative propulsion systems
> Low Energy consumption via lowering resistances
> Supply chains for BEVs must be well-organized
> Vehicle manufacturing partners must be familiar with market conditions and regulations
> The center of gravity shifts – and becomes ever more important
> MAGNA: Your manufacturing partner for alternative propulsion system excellence
RANGE AND CHARGING ARE (STILL) CENTRAL ISSUES OF ALTERNATIVE PROPULSION SYSTEMS
Just as in the first electrification period 120 years ago, maximum reach and charging duration are still the key issues of the second electrification period today. Customers are now used to driving ranges of 700 kilometers or more, only interrupted by a fuel stop of just a few minutes. Many BEV drivers find it simply unacceptable that to drive only 300 kilometers, BEVs require 30 minutes of waiting time for a full charge. They subsequently charge their vehicles “on-the-go,” whenever the opportunity emerges. A BEV manufacturer able to increase maximum driving ranges while significantly lowering charging durations will have an edge in the competition for global market shares and think about alternative propulsion systems.
The EV battery and its charging behavior are key to solve these two issues. As the race for the most competitive battery cell system is still open, there remains a lot of research and development (R&D) and subsequent testing to do. Both new and existing battery technologies require extensive testing and validation efforts, so automotive manufacturers eager to stay on top of the technological race should consider cooperating with a strong automotive manufacturing partner who owns separate battery testing grounds. This will result in significantly shorter development times and market entry. Modern lithium-ion batteries with liquid electrolytes can be further developed into other systems (e.g., solid-state batteries), promising higher energy density, reduced installation space and weight, and constant maximum range.
Alternative propulsion systems - charging strategies for electric batteries need to be developed
Aside from size and energy density, electric batteries also require a suitable charging strategy. Such a proper charging strategy is a key element of a successful overall operating strategy - for one key reason: The actual charging time of a battery strongly depends on whether and how the battery can handle constantly high charging power. BEV owners may be disappointed if the promised power peaks are only met for around 20 to 30% of the total charging duration and are then halved or even reduced to 33% power because the battery cannot handle them. This can increase both charging times and user frustration and hurt the image of both the manufacturer and BEV technology in general.
If charging voltages are to remain on a constantly high level throughout the entire charging process, manufacturers need an intelligent battery charging strategy coupled with a sophisticated thermal management system. The key lies in implementing appropriate counter measures to prevent overheating in the first place, through quick heating at the start or specific cooling measures during the charging process, for example. This way, the charging time can be reduced.
Intelligent operational strategies by optimized electric battery charging
Optimized charging strategies also allow manufacturers to implement a successful operational strategy. Such a strategy can assist drivers in choosing the ideal time to charge the battery. For example, the EV’s infotainment system could recommend the driver to immediately charge the vehicle after driving instead of charging it before the next drive. As the battery would still be heated from the use period, this method would save battery performance while optimizing charging currents, particularly during colder seasons. A complementary operational strategy could be implemented to reduce cooling time during the summer.
Additionally, the driver could be reminded to use the navigation system even on recurring, familiar routes to determine the next ideal time to charge as well as activate the thermal management system to initiate heating/cooling processes before arriving at the charging station.
LOW ENERGY CONSUMPTION VIA LOWERING RESISTANCES
There is
also ample potential to reduce energy consumption while driving. Efficiency
can be increased by lowering driving resistances, like an aerodynamic car body
to reduce air resistance, the most important metric at speeds of 70km/h or
higher. Further potential lies in rolling resistance, which is not only
influenced by tires supplied by the tire manufacturer, but also significantly
by frictional resistance in the entire powertrain chain: electric motor,
reduction gears, differentials, wheel bearings - all of these must be
considered in the development of the BEV so as not to waste precious battery
power.
A competent
automotive manufacturing partner of alternative propulsion systems will not
only provide the completely electrified powertrain including electronic
control, but should also possess the capabilities and infrastructure to test
and validate their propulsion system for all road and load scenarios and
evaluate the mechanical properties and energy currents under various
conditions.
Smart thermal management is important
Electric and
electronic components (E/E components) need to be trimmed for minimal power
usage and maximum efficiency. The inverter, a device that converts the direct
current (DC) from the battery into alternating current (AC), plays a major role
in ensuring said efficiency.
To build an
energy-efficient vehicle, its interior thermal management (how the
interior is heated and/or cooled) plays an important role.
With ICE’s,
the heat generated by the engine is used as a free source of heat for the
interior. An EV’s powertrain on the other hand hardly produces excess heat and
this is key for the exceptional efficiency of BEVs, it is not enough to keep
passengers warm. And while it is fairly simple to implement electrical interior
heating on a technical basis, its energy consumption will reduce an EV’s
maximum driving range, especially during cold seasons.
The electric
thermal pump is an efficient solution for this dilemma. It uses the residual
heat from outside the car to increase temperatures inside the car. If a BEV
employs smart thermal management and prepares its interior before departure,
the power consumption for heating can be lowered significantly, leading to a
longer range in the cold seasons. The more sophisticated a BEV’s operational
strategy is, and the more efforts are placed on its thermal management, the
more reliable it is in sustaining its maximum range.
SUPPLY CHAINS FOR BEVs MUST BE WELL-ORGANIZED
Cooling the
vehicle interior during warm seasons is also part of every thermal management
concept. In BEVs, this is handled by an electric A/C compressor.
Although A/C has a lower energy demand than heating, a well-controlled A/C
compressor and A/C system with optimized thermal management go a long way to
reduce total energy consumption of a BEV. Still, the A/C system needs to be
powerful enough to prevent fogged window panes even under difficult conditions.
Even the
best manufacturing partners and suppliers are useless if supply chains are
insufficiently organized. With the semi-conductor crisis, Covid, and the war in
Ukraine, it is clearer than ever that supply and production chains need to be
agile and flexible to withstand rapid regional and global changes. Employing
numerous regional sub suppliers for base components is vital for ensuring secure
supply chains and softening the impact of supply shortages. This way, a
considerate development and production partner can keep the supply of vehicle
components as well as complete vehicles running.
VEHICLE MANUFACTURING PARTNERS MUST BE FAMILIAR WITH MARKET CONDITIONS AND REGULATIONS
The complete
vehicle development of a BEV in particular requires a lot of preparatory planning by the
manufacturing partner. The future effects on materials, global laws and
homologation regulations, production, and distribution must be considered
starting in the concept phase. Only if manufacturers are aware of the different
conditions each market operates under will they be able to prevent later
mistakes – and the costs of fixing them.
Aside from
cost transparency and cost supervision, end customer’s satisfaction
plays an important role. End customers will only develop brand loyalty if they
are satisfied with their purchase. Providing a positive complete package for
new customers is imperative, especially as they shift from ICEs to BEVs.
Ultimately, the total user experience should leave BEV drivers more satisfied
than with their old ICE. The EV should be more pleasant to use and drive than
an ICE – and features like seamless (and soundless) acceleration out of a
standstill are important for a vehicle, but not enough advantages for everyday
use.
THE CENTER OF GRAVITY SHIFTS - AND BECOMES EVER MORE IMPORTANT
If BEVs want to convince potential new customers, they must persuade them with superior overall driving dynamics. Here, BEVs have an inherent disadvantage towards ICEs. Their large and heavy battery increases the car’s total weight by several hundred kilograms compared to an ICE of similar dimensions. This has a negative effect on handling and cornering, and may cause the EV to feel rigid and sluggish. As the additional weight can hardly be mitigated, the question shifts towards the center of gravity. What should the battery look like and where should it be placed in the vehicle?
As EV batteries can be produced in many different dimensions and shapes, engineers can place the battery in a way that the vehicle’s weight is evenly distributed between the front and rear axles. Subsequently, the car’s wheelbase is increased in length while car body overhang is reduced. Both measures further harmonize cornering despite a higher car weight.
Ideal battery placement ensures maximum driving security
Additionally, battery placement also has a large impact on driving security. Cooling must be ensured under all conditions and the battery must not be damaged, even under maximum stress. Battery tests employ worst case scenarios, such as accidents where the battery is put under enormous mechanical forces or overloading scenarios to determine the battery’s durability under thermal overuse, degassing, or fire. This ensures that countermeasures can be implemented during BEV development and production to prevent potential accidents in the first place.
Ultimately, the BEV must be comfortable to drive, especially for customers who have only switched recently to alternative propulsion vehicles. Although the rapid standstill acceleration is impressive for both driver and passengers, it also puts great demand on an EV’s control system. The engine must react accordingly and predictably if the driver accelerates, which is important for ranging maneuvers during parking as well as driving under rainy or snowy conditions. Driving control systems must meticulously reduce the torque of the electrical engine(s) to help the driver stay on track in case of wheel slip and exert specific braking overrides, if necessary. In order to properly calibrate this complex coordination between electronic and mechanical systems, a lot of experience and knowledge of driving dynamics is needed. A capable contract manufacturing partner usually has experienced developers, who can meticulously and efficiently plan and test for a secure car.
Braking and acceleration must provide a consistent experience for ICE drivers
A typical problem for the perceived drivability of a BEV is the braking feel. BEVs hardly deploy their wheel brakes, but rather use the engine to generate braking power as well as electricity through recuperation. This means that the energy created by braking can be repurposed by the vehicle battery instead of being emanated as useless heat emissions. In 90% of use cases, the braking effect of recuperation is sufficient. However in the remaining 10%, the car will also activate the wheel brakes for deceleration.
A successful transition from one braking system (electric) to the other (mechanical) is crucial for the driver's braking feel and thus for the perceived safety of the car. The braking effect and pedal feel must remain predictable and linear even when the wheel brakes are also used, so that the driver can apply the deceleration power correctly and comfortably - an often-neglected secondary aspect, but all the more of a challenge for the developers and during testing.
MAGNA: YOUR MANUFACTURING PARTNER FOR ALTERNATIVE PROPULSION SYSTEM EXCELLENCE
At Magna, we have more than 30 years of experience with the development of alternative propulsion systems and the special and specific issues of electric mobility. All challenges of EV planning, engineering, construction and (serial) production are met by Magna in a reliable and cost-efficient manner. By steadily improving our capabilities and foresighted investments, Magna has become one of the global leaders of BEV development and problem solving – from which every automotive manufacturer can profit.
Do you want to bring your own automotive vision on the road?
Contact us at: discovermore.magnasteyr@magna.comStay connected with Inside Automotive!

Helfried Müller
Helfried Müller currently works as a Product Manager of Alternative Powertrain System Integration at Magna Steyr. Prior to his current role, he worked as Head of Alternative Powertrain Systems R&D and Project Manager for Alternative Mobility. He started his career at Magna Steyr - former Steyr Daimler Puch - as a Design Engineer in 1998. Helfried Müller holds a degree in Information Technology.
We want to hear from you
Send us your questions, thoughts and inquiries or engage in the conversation on social media.
Related Stories
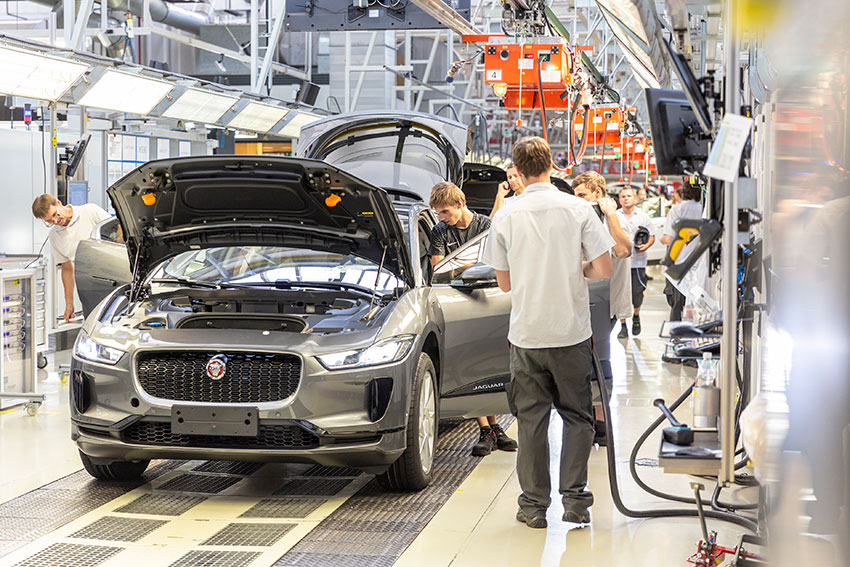
Flexibility is Key – Challenges and Solutions of Vehicle Assembling in a Multi-OEM-Production
Blog
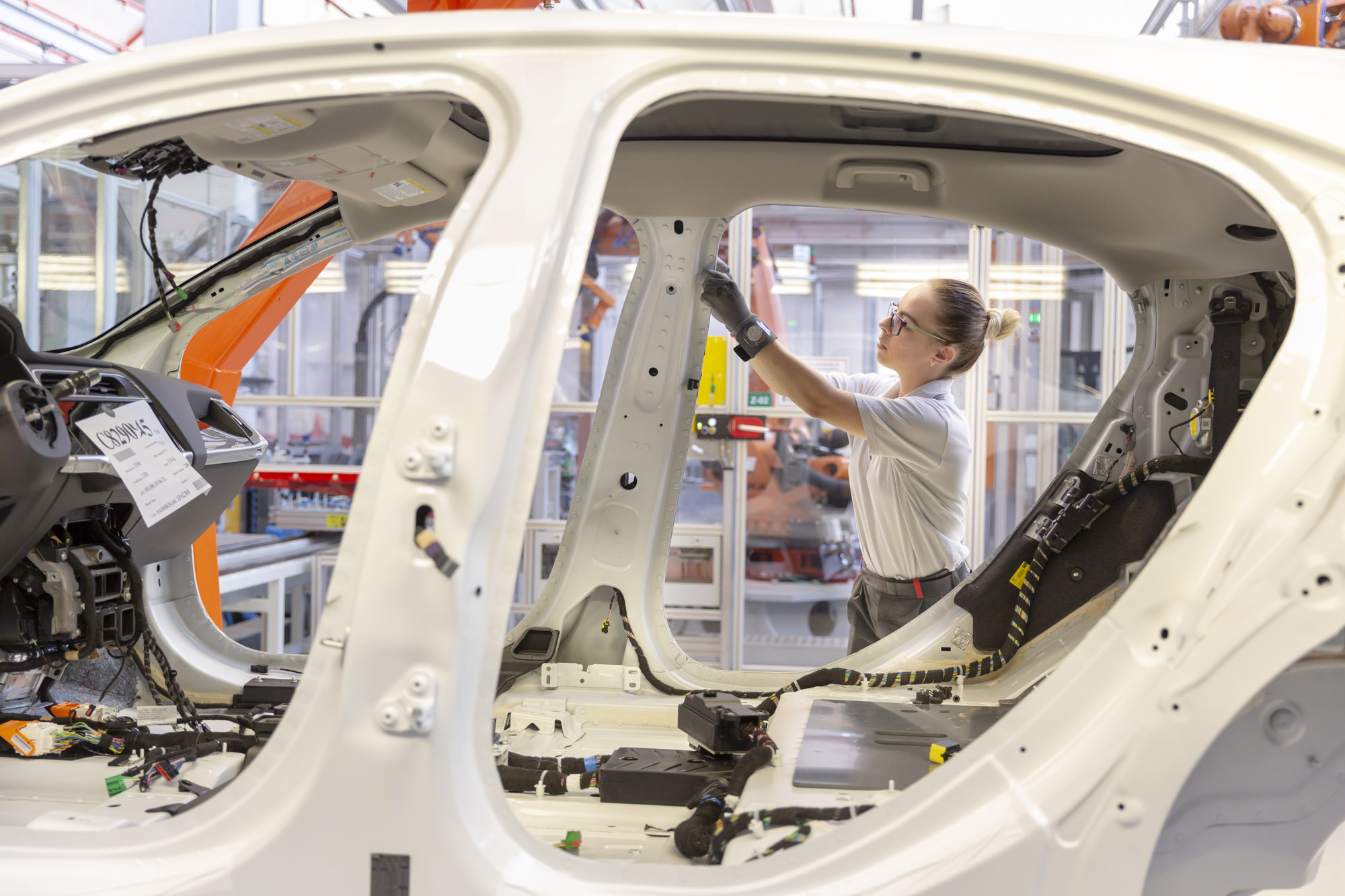
Specific Know-How and Geo Skid: How a Multi-OEM Contract Manufacturer Ensures Peak Quality and Flexibility From Body-in-White Onward
Blog
Stay connected
You can stay connected with Magna News and Stories through email alerts sent to your inbox in real time.